Service
Electronics
Electronic cnc machine tool support

Assistec offers electronic assistance on CNC machine tools providing a complete service.
Electronic assistance on machine tools is effective and efficient thanks to the service department, which carries out a careful preventive telephone diagnosis. The extensive stock of electronic spare parts allows the problem to be solved as early as the first technical intervention.
Thanks to the skills and experience of our technicians, we are able to minimise machine downtime.
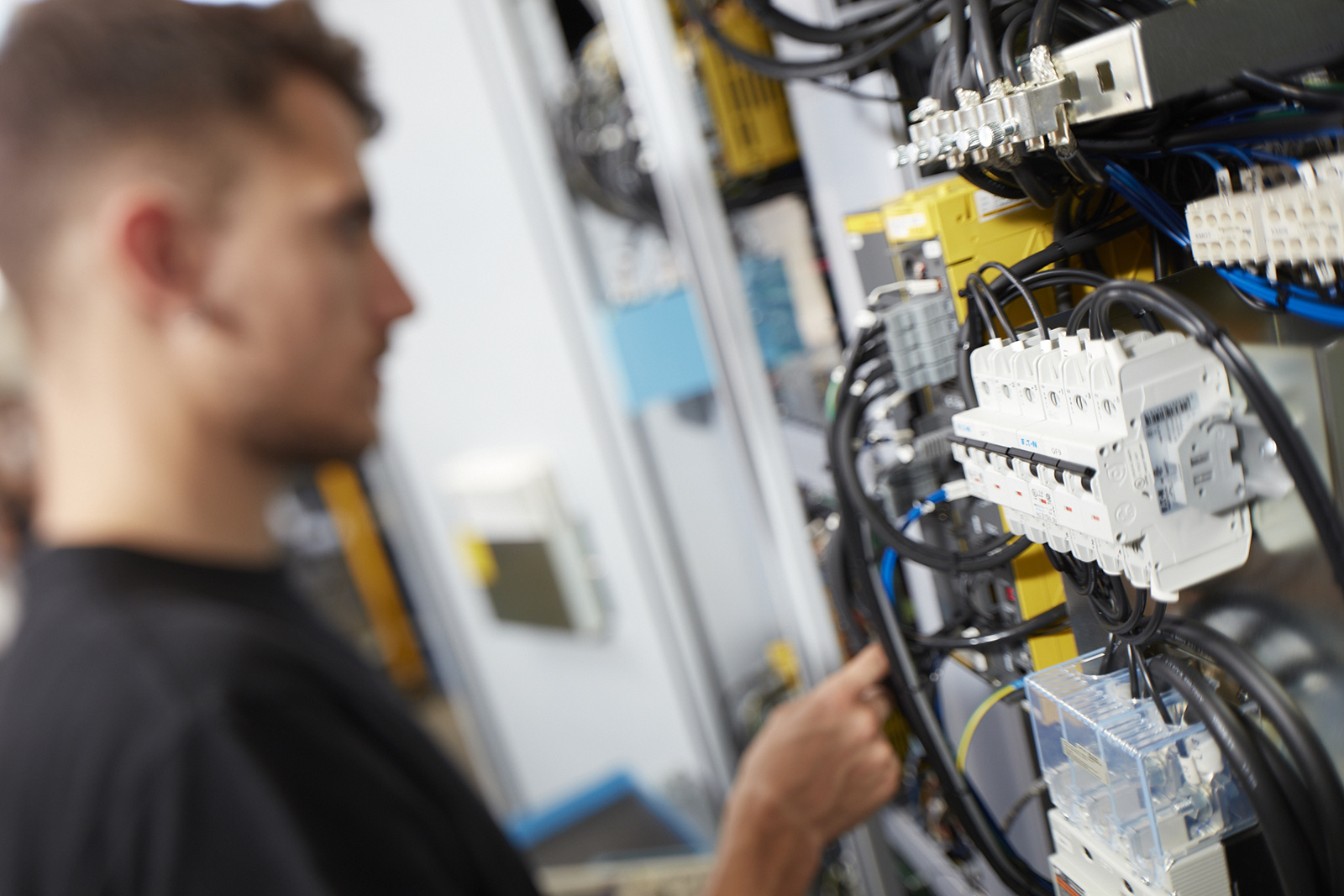
Our electronic support services include:
- Service on machine tools with Fanuc, Mitsubishi electronics fitted by European and Asian manufacturers.
- Service on axis and spindle drives and motors of any series.
- Interfacing third-party robots for workpiece loading and unloading, push bar systems on lathes and CNCs and interfacing of gantry loaders, assessing any customer interfacing requirements
- Modifications to machine PLC logic for safety according to current regulations, implementation of automatic doors, conveyor belts, increase in M codes for machine operator (rigid tapping, etc.) Inspection of your obsolete machine tool for safety implementation in accordance with regulations
Our electronic service technicians are able to perform
Retrofit operations on lathes and machining centres involving the replacement of all electronic, electrical, measuring systems and the introduction of new automatisms and control systems inside the machine with subsequent final testing
.jpg)
Specifically, we carry out electronic retrofits on Doosan turrets.
Our team of technicians can replace the Pro-Motion or Vision drive/motor with a new Fanuc-branded handling system.
Leading to the following advantages:
- Modern and highly reliable technology
- Availability of spare parts within 24/48 hours
- Cost-effective compared to the Pro-Motion/Vision system.
- Simplification in handling day-to-day turret-related challenges, such as accidental collision and the subsequent need for phasing
We have identified a number of machine models on which this system can be installed: Doosan Puma 200, Doosan Puma 230, Doosan Puma 240, Doosan Puma 300, Doosan Puma 1000, Doosan Puma 2100, Doosan Puma 2600, Doosan Puma 3100, Doosan Puma TT1300, Doosan Puma TT1800, Doosan Puma TT2100, Doosan Puma TT2500, Doosan Puma GT 2100, Doosan Puma GT 2600, Doosan Puma GT 3100, Doosan Lynx 2100, Doosan Lynx 2600.
Retrofit on Doosan machines
We perform retrofits on Doosan machines to upgrade and improve functionality. Work includes replacing the motor, drive and cables, modifying the PLC and creating reset procedures. The benefits are considerable: modern and reliable technology, reduced downtime with spare parts available within 24/48 hours, and cost savings. In addition, turret management has been simplified, reducing operational complications.
Retrofit on Lapping Machine
We recently performed a major retrofit on a lapping machine, significantly improving its performance and adapting it to new production requirements. During this process, various mechanical and electronic interventions were carried out, replacing defective components, adapting supports and realigning for maximum precision.
In addition, the following work was carried out: software updates including HMI, Industry 4.0 connection, software rewriting and reactivation of the quality control system
Robot drive repair
We recently completed the repair of the servo drive of a Fanuc robot, bringing it back to full operational efficiency. The work began with the dismantling and inspection of the damaged component to identify the cause of the malfunction.
Subsequently, our technicians spent time and energy repairing and overhauling the servo drive, using state-of-the-art tools and following strict quality standards.
Once repaired, the drive was thoroughly tested to ensure full functionality of the robot. Finally, the component was reassembled on the robot and tested at the customer's site to ensure that the production cell would be operational again.
With a view to reducing machine tool maintenance costs and a controlled spending budget over time, we also offer our customers preventive maintenance services that allow them to schedule downtime and plan interventions.
This extends the average life of the machines and reduces downtime due to sudden breakdowns.
How do we do this?
Our standard electronic service contract includes
- Electronic Service hour package of your choice discounted from list rates;
- 8 hours of extra service, i.e. an electronics technician on call for one day;
- The activities the technician will be able to do include: machine inventory, back-up, battery check and replacement, maintenance, and more;
- Priority telephone help desk.
Would you like to know in detail the services our Electronic Repair Workshop can offer? Fill in the form below!